玻璃工业节能减排:世界首个使用100%氢气的玻璃工厂来了
- 发布人:管理员
- 发布时间:2021-08-31
- 浏览量:594
英国政府的氢气战略发布一周后,在利物浦市地区开始了使用100%氢气生产浮法(片)玻璃的试验,这在世界上还是首次。
通常在生产过程中使用的天然气等化石燃料将被氢气完全取代,这表明玻璃工业可以显著减少碳排放,并朝着实现净零的目标迈出一大步。
试验在英国玻璃企业皮尔金顿(Pilkington)的圣海伦斯工厂进行,该公司于1826年在这里首次开始制造玻璃。为了让英国脱碳,几乎所有经济部门都需要彻底转型。工业占英国所有温室气体排放的25%,如果这个国家要达到“净零”,减少这些排放是至关重要的。
然而,能源密集型产业是最难应对的挑战之一。工业排放,比如玻璃制造,尤其难以减排——通过这项试验,我们离克服这一障碍又近了一步。开创性的“HyNet工业燃料转换”项目由Progressive Energy牵头,氢气由BOC提供,将为HyNet的低碳氢取代天然气提供信心。
这被认为是世界上第一个在活浮法(片)玻璃生产环境中100%氢燃烧的大规模演示。英国皮尔金顿试验是英格兰西北部正在进行的几个项目之一,旨在测试氢在制造业中如何取代化石燃料。今年晚些时候,HyNet的进一步试验将在联合利华(Unilever)阳光港(Port Sunlight)举行。
这些示范项目将共同支持玻璃、食品、饮料、电力和废物等行业转化为使用低碳氢,以取代它们对化石燃料的使用。两项试验均使用BOC提供的氢。2020年2月,BEIS通过其能源创新项目向HyNet工业燃料转换项目提供了530万英镑的资金。
“HyNet将为西北地区带来就业和经济增长,启动低碳氢经济。我们专注于减少排放,保护西北地区现有的34万个制造业就业岗位,并创造6000多个新的永久性就业岗位,使该地区走上成为世界清洁能源创新领导者的道路。”
NSG集团旗下皮尔金顿英国有限公司的英国总经理Matt Buckley说:“英国皮尔金顿和圣海伦斯再次站在工业创新的最前沿,在浮法玻璃生产线上进行了世界上首次氢气试验。”
“HyNet将是支持我们脱碳活动的重大一步。经过数周的全尺寸生产试验,成功地证明了使用氢气安全有效地运营浮法玻璃工厂是可行的。我们现在期待HyNet的概念成为现实。”
现在,越来越多的玻璃生产企业开始加大对节能减排技术的研发创新,利用新型熔制工艺技术手段来控制玻璃生产能耗。小编就来给大家列举三个。
一、全氧燃烧技术
全氧燃烧是指在燃料燃烧的过程中用氧气代替空气助燃的过程,该项技术使空气中约 79%的氮气不再参与燃烧,可以提高火焰温度,加快燃烧速度。此外,全氧燃烧时废气排放量约为空气燃烧时的 25% ~ 27%,熔化率也有明显的提高,可达到 86% ~ 90%,这意味着获得相同数量的玻璃需要的熔窑面积减小了。
工程案例
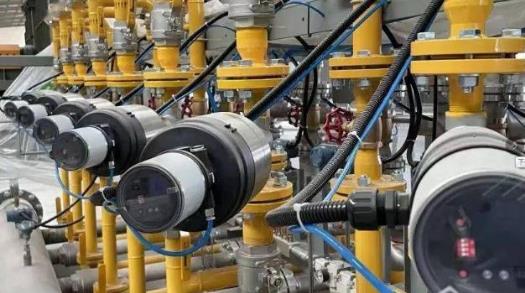
2021年 6月,作为四川省工业重点扶持项目,四川康宇电子科技迎来其全氧燃烧窑炉主体工程正式竣工,基本具备移火升温条件。该建设项目为“超薄电子盖板玻璃基材、 ITO导电玻璃基材”,是目前国内最大型的一窑两线全氧燃烧浮法电子玻璃生产线。
该项目熔化部采用了 全氧燃烧 +电助熔技术,依靠氧气和天然气燃烧,并通过电助熔等方式来进行辅助熔化,不仅可以节约15%~25%的燃料使用量,还可以增加窑炉单位面积的出料量 ,提高25%左右的生产效率。此外,还可以减少废气的排放,降低60%以上因为燃烧而产生的NOx,CO₂等氮氧化物的比例,从根本上解决排放源头的问题!
二、 烟气脱硝技术
烟气脱硝技术原理是利用氧化剂将NOX氧化成NO2,生成的NO2再用水或碱性溶液吸收,从而实现脱硝。该技术主要分为选择性催化还原脱硝(SCR)、选择性非催化还原法脱硝(SCNR)和湿法烟气脱硝三种。
工程案例

目前,在废气治理方面,沙河地区的玻璃企业基本都建成 SCR脱硝设施,采用氨、 CO或碳氢化合物等作为还原剂,在氧气存在的条件下将烟气中的 NO还原为 N2。
河北沙河安全实业有限公司1-8#玻璃窑炉烟气脱硫脱硝除尘备用线EPC项目,自2017年5月份建成投运以来,环保系统运行稳定,烟气中污染物排放浓度可达颗粒物小于10 mg/N㎡、二氧化硫小于50 mg/N㎡、氮氧化物小于100 mg/N㎡,污染排放指标长期稳定达标。
三、余热发电技术
玻璃熔窑余热发电,是通过余热锅炉回收玻璃熔窑废弃余热中的热能发电的技术。 将锅炉给水加热生产出过热蒸汽,然后过热蒸汽送到汽轮机内膨胀做功,将电能转换成机械能,进而带动发电机发电。该项技术不仅节能,还有利于环境保护。
工程案例

咸宁南玻于 2013年投资 2300万元建设余热发电项目,并于 2014年 8月并网发电成功。近年来,咸宁南玻一直在利用余热发电技术实现玻璃行业的节能减排。据悉,咸宁南玻余热电站 平均发电量约为 4000万度,折标系数按发电标准煤耗 0.350kg标准煤 /kWh,二氧化碳排放量 2.62kg/kg标准煤计算,所发电量相当于节约 1.4万吨标准煤,减排 3.67万吨二氧化碳!
“碳达峰”、“碳中和”的目标任重而道远,玻璃企业仍需继续努力,升级玻璃工业新技术,调整技术结构,推动我国“双碳 ”目标的加速实现。相信在科学技术的发展之下,在众多玻璃生产企业的深耕之下,玻璃行业一定能够实现高质量发展、绿色发展和可持续发展!